Construction projects use various scheduling techniques to plan and track progress. One effective method for repetitive work is line of balance scheduling. It helps ensure a steady workflow across multiple units or locations, such as floors or housing units.
Unlike traditional Gantt charts, line of balance focuses on balancing crews, sequencing tasks efficiently and avoiding trade stacking. This makes it particularly useful in high-volume, high-efficiency construction settings like commercial buildings, roads or apartment complexes.
What Is Line of Balance Scheduling in Construction?
Line of balance scheduling in construction is a method used to coordinate repetitive tasks across multiple locations or units. In this construction scheduling method, units are the individual, repeatable segments of work—like floors in a building, apartments in a block or sections along a pipeline—where the same activities are performed sequentially.
This emphasizes the continuous and balanced flow of work to prevent delays and minimize idle time. Each trade progresses from one unit to the next in a set sequence, allowing for efficient resource allocation and reduced conflicts. This technique is ideal for projects with repeating structures, like high-rise buildings or linear infrastructure such as railways and pipelines.
Line of balance scheduling impacts a Gantt chart in construction by introducing a production-based planning perspective that complements the task- and time-focused structure of a Gantt chart. It’s particularly useful for repetitive work—like floor-by-floor construction in high-rise buildings or housing developments—by aligning tasks across units or locations in a sequential, consistent flow.
When integrated into ProjectManager’s Gantt chart, the line of balance scheduling influences how tasks are sequenced and timed. Instead of listing tasks only by phase, the Gantt chart reflects the repetitive nature of the work, showing overlapping or staggered activities that repeat across multiple units or sections. This helps identify potential bottlenecks and ensures crews move smoothly from one work area to the next without idle time or clashes between trades. By coordinating the line of balance with a Gantt chart, construction teams can visualize both time and production flow, resulting in a more efficient, balanced and realistic project schedule.
Our software makes it easy to stagger tasks—such as framing, electrical or plumbing—across different floors or buildings, reflecting the flow and rhythm of the line of balance. You can set dependencies to ensure one crew finishes in one area before another starts, avoiding trade stacking or delays.
Since our Gantt chart integrates with workload charts, resource planning and dashboards, any adjustments to the production flow are instantly reflected across the project, helping managers balance resources, maintain consistent output, and keep the construction schedule on track. Get started with ProjectManager today for free
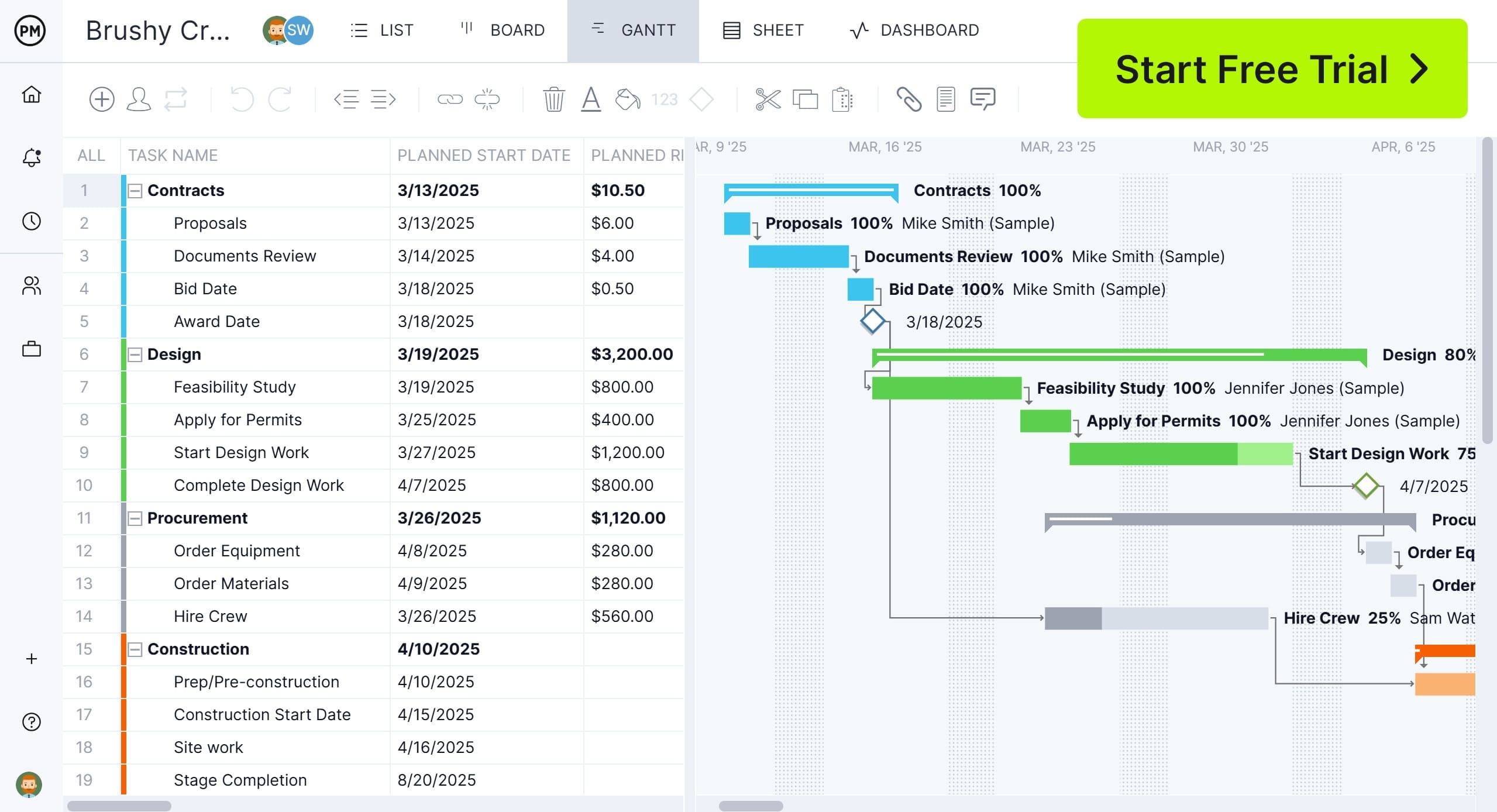
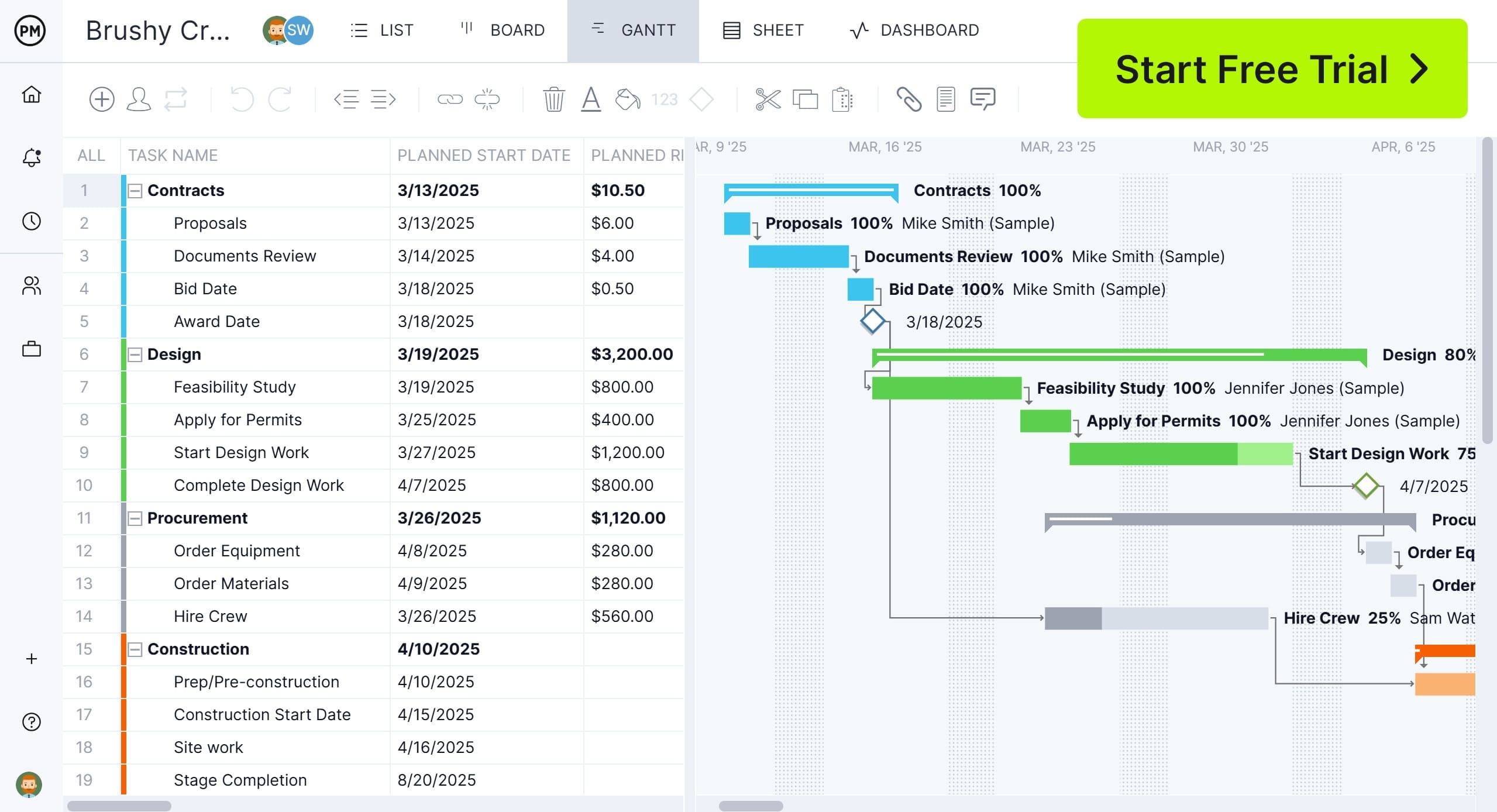
Line of balance scheduling works by mapping repetitive construction tasks—such as framing, plumbing and finishing—against both time and location. Each crew follows a steady rhythm, moving seamlessly from one unit to the next, based on calculated production rates. This approach ensures that work flows smoothly without interruptions or bottlenecks. The method emphasizes timing, spacing and sequence to maintain balance across units.
The true power of this method emerges when these elements are combined into a time–distance diagram: the Line of Balance chart. It highlights potential bottlenecks or gaps, reveals where crews may overlap or idle, and provides planners with a clear view of workflow continuity. In the next sections, we’ll explore how this essential chart functions and why it’s so effective.
What Is a Line of Balance Chart?
A line of balance chart is a visual scheduling tool used to track the progress of repetitive construction tasks across time and units. The chart plots time on the horizontal axis and units (e.g., floors or sections) on the vertical axis. Each line represents a trade’s progress, showing when and where each activity occurs. It helps detect overlaps, delays or idle periods. Project managers use this chart to optimize crew movement, maintain flow and improve schedule reliability.
- Time (X-axis): Represents the duration of the project in days or weeks
- Units (Y-axis): Represents repetitive areas such as floors, rooms or buildings
- Activity Lines: Diagonal or horizontal lines showing progress of trades across units over time
- Start and Finish Points: Show when each trade begins and ends work on a unit
- Slopes of Lines: Indicate the pace of work—steeper lines mean faster progress
- Gaps or Overlaps: Reveal idle time or potential trade conflicts that need rescheduling
Line of Balance Chart Example
This line of balance chart example illustrates a real‑life scenario for scheduling repetitive construction tasks in a 5‑story building. The project includes framing, plumbing, electrical, finishing and HVAC work on each floor. Start and finish dates for each task are calculated to maintain crew flow and minimize downtime.
In this chart, you’ll see 10 upward-sloping diagonal lines—two for each trade: framing, plumbing, electrical, finishing and HVAC/mechanical:
- Each paired line marks the start and finish of a single trade on each floor, forming a clear “envelope” that visually shows how long work takes per floor.
- The gap between each pair indicates the duration of that trade’s work on a given floor—longer gaps mean longer task duration.
- The spacing between different trades’ envelopes reveals how crews are staggered, ensuring one trade wraps up before the next begins on any given floor.
- Lines that run parallel across floors confirm consistent pacing and steady production rates.
- Any lines that come too close or cross-highlight potential bottlenecks or resource conflicts signal where adjustments may be needed.
This dual‑line “start–finish envelope” setup gives readers a clear, visual understanding of both task timing and crew sequencing—exactly what makes LOB charts so powerful for repetitive construction workflows.
Related: 18 Best Construction Scheduling Software of 2025
Benefits of Using the Line of Balance Technique for Construction Scheduling
Line of balance scheduling offers a range of advantages for construction projects involving repetitive work. By focusing on flow, timing and sequencing, this technique enhances coordination between trades, reduces waste and improves overall productivity. It also provides a clear visual overview of progress, which helps project managers make informed scheduling decisions throughout execution.
Reduces Idle Time for Labor and Construction Equipment
Line of balance scheduling reduces idle time by organizing tasks so that crews and equipment move continuously from one unit to the next without waiting. This steady flow minimizes downtime caused by delays, access issues or trade interference. As a result, productivity increases and the cost of keeping workers or machines inactive is significantly reduced.
Facilitates Resource Scheduling
This technique helps allocate labor, equipment and materials with precision. Because each activity is tied to a specific location and time, project managers can plan deliveries and crew assignments accordingly. Resource scheduling becomes more predictable, which minimizes the risk of shortages or surpluses and keeps the project on budget and on track.
Improved Workflow Efficiency
Line of balance promotes a structured and repeatable approach to construction, allowing work to progress smoothly across identical units. This consistency enhances coordination between trades and limits disruption. Since tasks are timed to follow one another with minimal delay, workflow becomes more efficient, enabling teams to meet deadlines and avoid cascading delays.
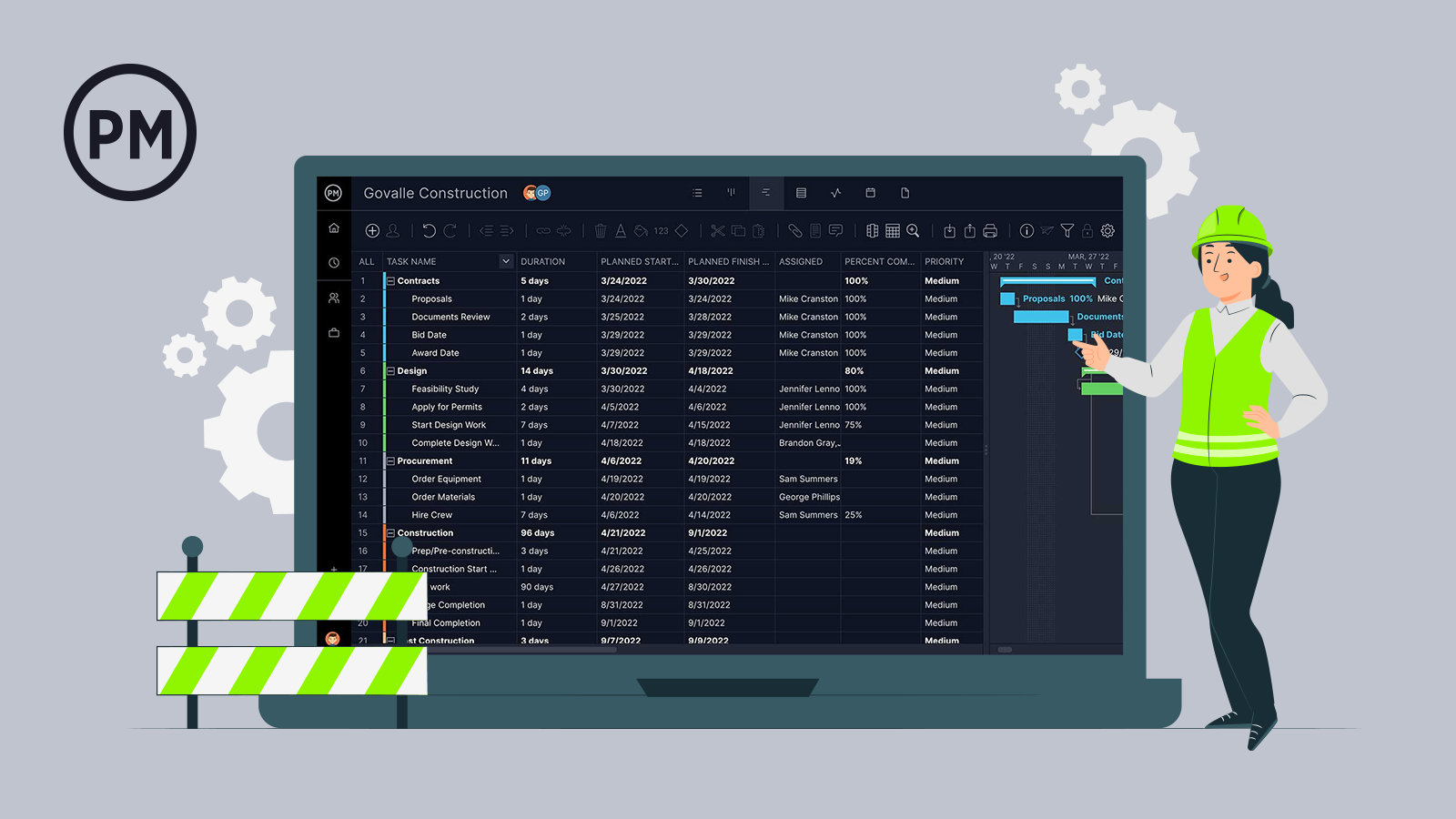
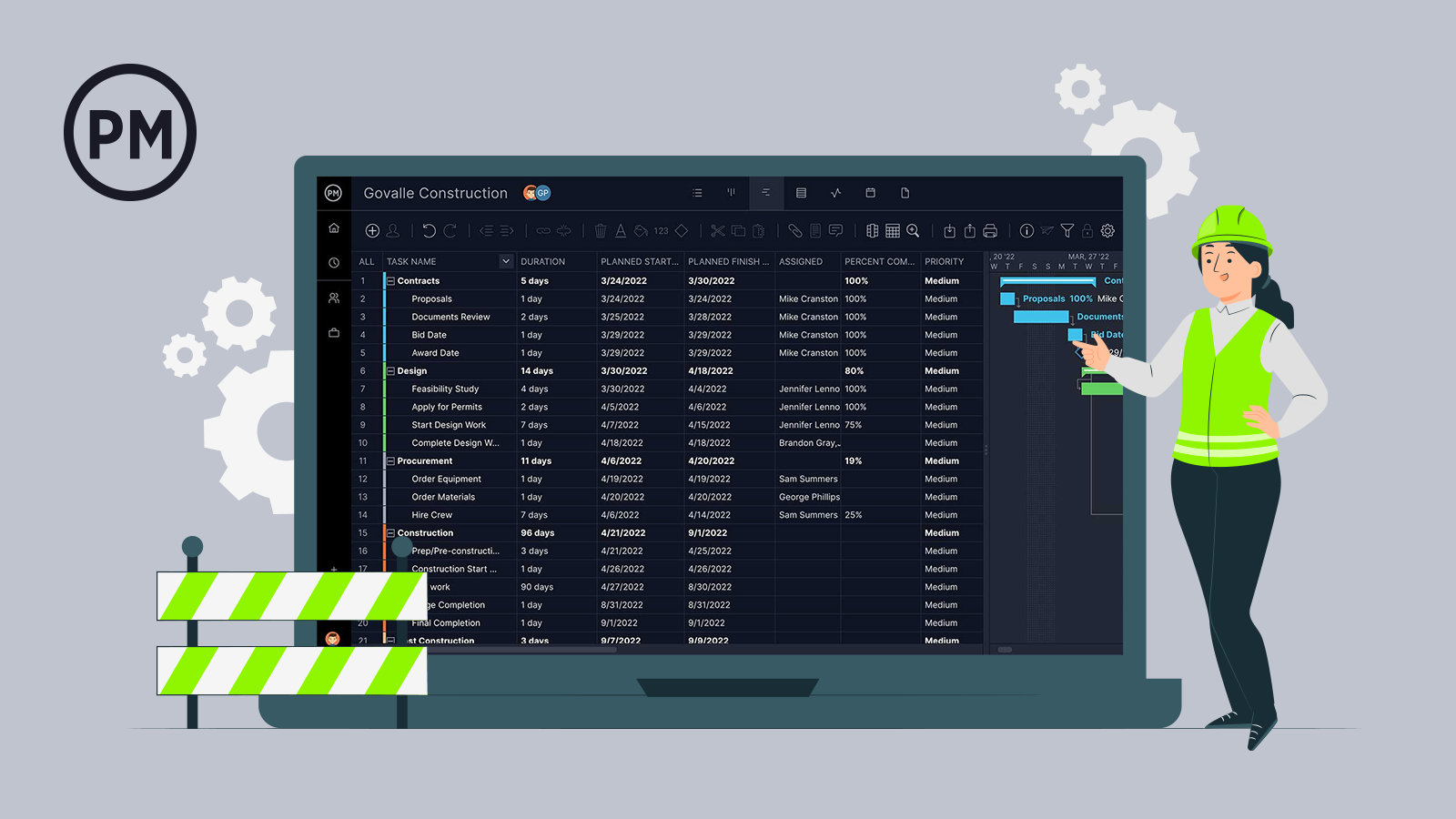
Get your free
Construction Schedule Template
Use this free Construction Schedule Template to manage your projects better.
Who Participates in the Line of Balance Scheduling Process?
The Line of Balance scheduling process involves key project stakeholders who contribute to planning, sequencing, and executing repetitive tasks efficiently. These participants typically include the project manager, who oversees the overall schedule; construction schedulers or planners, who develop and maintain the LOB chart; and trade contractors, who provide input on task durations and crew availability. Additionally, site supervisors, logistics coordinators and sometimes clients or owners are involved to ensure alignment on milestones, resource flow and project goals.
How to Implement the Line of Balance Scheduling In a Construction Project
Implementing line of balance scheduling involves several structured steps to ensure efficient repetition, resource coordination and timing. Below are the foundational actions required to apply this technique successfully in projects with repetitive tasks.
1. Identify Repetitive Activities
Start by listing all tasks that will occur in multiple units, such as framing, plumbing, electrical or finishing. These repetitive activities form the backbone of the LOB schedule. Breaking down work into repeatable segments ensures each crew follows a predictable pattern and makes flow mapping possible.
Here are illustrative examples to explain the tasks for a unit. In this case, the unit is each floor in a 5-story building. Then, the tasks for each task sequence are broken down, such as framing, plumbing, electrical work and HVAC and mechanical work.
- Framing (Floor 1): Build floor joists, wall studs, roof trusses and exterior sheathing—then repeat the exact sequence on Floor 2, Floor 3 and beyond.
- Plumbing (Floor 1): Rough-in drain lines, risers and water supply pipes in each bathroom and kitchen—then replicate on all higher floors.
- Electrical (Floor 1): Run conduits, install junction boxes, pull wiring and set up breaker panels—repeated identically on each floor above.
- Finishing (Floor 1): Hang drywall, tape and texture, prime and paint walls, then install trim—each floor follows this process in turn.
- HVAC/Mechanical (Floor 1): Install ductwork, place registers and diffusers, and set up branch piping—then perform the same HVAC install sequence on every floor.
These examples demonstrate how each task type is performed in the same way on every floor, which acts as a unit, forming the repetitive cycles essential to line of balance scheduling.
2. Identify Task Dependencies and Determine Task Sequences
Analyze how activities relate—for example, plumbing must follow framing and finishes depend on MEP rough‑ins. Establish logical task sequences and dependencies. Defining these relationships helps maintain continuity and avoid scheduling conflicts as crews move between units.
3. Estimate Task Duration
Calculate the time each repetitive activity takes per unit based on production rates and crew capacity. Use historical data, crew experience or pilot runs. Accurate duration estimates are essential to determine pacing, crew spacing and prevent idle or overlapping work.
Related: 20 Free Excel Construction Templates
4. Define the Number of Repetitions
Determine how many times each activity will repeat, such as the number of floors, apartments or sections. This gives you the total count of units for each task and sets the Y‑axis scope of the LOB chart. It’s essential to visualize the full workflow span.
5. Estimate the Total Project Duration
Based on task durations, number of repetitions and sequence spacing, calculate the total time to complete all units. Incorporate buffers for handoffs, resource changes or site constraints. This overall duration forms the project timeline on your LOB chart.
6. Draw the Line of Balance Chart
Plot time on the horizontal axis and work units on the vertical axis. For each repetitive activity, draw a line using calculated start and finish times for every unit. The slopes reflect production rates, while spacing highlights sequence and pace. Visual representation helps identify out‑of‑sync crews or pacing issues before they become problems.
7. Optimize the Schedule
Analyze the chart for overlapping lines, tight stacking or idle gaps. Then adjust crew start times or pacing to smooth flow and prevent interference. Re‑sequence tasks or reallocate resources as needed to eliminate bottlenecks. Continuous refinement helps maintain steady crew movement, maximize productivity and minimize downtime.
Free Construction Scheduling Templates
While construction projects are best handled with project management software, which is better equipped to deal with the dynamic nature of the work, there are free templates for those not ready to upgrade. We have over 100 free project management templates for Excel and Word that can help with every aspect of managing a project. Here are just a few examples that assist with construction project management.
Punch List Template
Download this free punch list template to track incomplete, incorrect or outstanding tasks that must be addressed before final project closeout. It includes items such as minor repairs, missing finishes, or quality issues, along with assigned responsibilities, deadlines for correction and status updates. This template ensures all work meets contract standards before handover, facilitates clear communication between contractors and clients, and helps organize the final inspection and approval process efficiently.
Action Plan Template
Use this free action plan template in construction to outline specific steps needed to achieve a project goal, resolve an issue or implement corrective measures. It includes tasks, responsible parties, deadlines, required resources and progress tracking. In construction, this template is especially useful for managing safety improvements, addressing delays, responding to inspection findings or executing quality control measures. By clearly organizing who does what and by when, an action plan template helps ensure accountability, improve coordination and keep the project moving forward efficiently.
Gantt Chart Template
This free Gantt chart template is a visual scheduling tool that outlines the timeline of a construction project by displaying tasks, start and end dates in a horizontal bar chart format. It helps project managers plan, coordinate and monitor each phase of construction—such as site preparation, foundation, framing and inspections—ensuring work is completed in the correct sequence. By using a Gantt chart template, teams can visualize the entire project schedule, track progress, identify potential delays and keep all stakeholders aligned throughout the construction process.
ProjectManager Is Advanced Construction Scheduling Software
ProjectManager is a better alternative to static templates because it offers a dynamic, real-time scheduling platform that eliminates manual updates, reduces errors and provides instant visibility into every aspect of a construction project. As advanced construction scheduling software, it excels in resource planning by integrating tools like availability settings, a centralized team page and a color-coded workload chart.
These features let managers assign tasks based on actual crew availability, visualize resource allocation at a glance and rebalance workloads before bottlenecks occur. Unlike templates that require constant manual input and offer limited insight, our intelligent resource planning keeps schedules realistic, crews productive and construction projects running smoothly from start to finish.
Watch our short video below to see more ways that our construction scheduling software can help support successful projects.
Manage Tasks With Multiple Construction Scheduling Views
Our multiple project views update in real time, giving construction teams the flexibility to manage schedules, tasks and resources in the format that works best for them. Whether using the Gantt chart for timeline planning and dependencies, the task list for daily job site execution, the kanban board for workflow tracking or the calendar view for milestone visibility, all views are fully synced—so updates in one view reflect instantly across the project.
This flexibility ensures that everyone—from project managers to foremen to subcontractors—can work in a format that suits their responsibilities while staying aligned with the broader construction plan, something no static template can achieve.
Track Projects With Real-Time Dashboards, Reports and Timesheets
Real-time data, automation and integrated tools offer a full picture of project performance. For a high-level overview, our real-time dashboards instantly show task progress, resource usage and schedule status, helping teams identify delays or issues as they happen. Customizable reports provide deeper insights into budget variance, labor productivity and milestone progress, tailored to stakeholders’ needs.
Meanwhile, secure timesheets ensure accurate time tracking, feeding directly into cost and schedule metrics. Together, these tracking tools enable proactive decision-making, greater accountability and a clear path to keeping construction projects on time and on budget.
Related Construction Project Management Content
A last planner system is a small part of the larger construction project management sector. For those who care to learn more about the big picture, follow these links to recently published articles on process, reporting and more.
ProjectManager is online construction project and portfolio management software that connects teams whether they’re in the office or out in the field. They can share files, comment at the task level and stay up to date with email and in-app notifications. Join teams at Avis, Nestle and Siemens who are using our software to deliver successful projects. Get started with ProjectManager today for free.